前回、私が「担当した記事では、「基本のキ、3S・カイゼンを怠っていないか?」と題して、事務部門やホワイトカラーの世界で案外カイゼンが定着していないことを指摘した。デジタルトランスフォーメーションは、デジタルを使った変革のダイナミックな反復継続である。
しかし、経営陣・管理者に、自分の担当工程の「ここ」を改善したい、と提案しても、全社的な改善はなかなか進まない。「今までこうやってきた。うまく進んでいる。だからこのままでいいや。」との姿勢から、否定的な対応をとられることも多いであろう。
今回は、具体的にシステム管理者が突き当たるであろう、変革のリードの仕方、変革への社内各所からの様々なニーズへの対応について考えてみる。
- 目次
- 1.カイゼンには、全社的なルールが必要
- 2.基幹システムが悪いのか
- 3.RPA、ノーコードツールには意外な落とし穴が
- 4.ぜひ導入を提案してほしい!リーンマネジメント
- 5.完全なスマート化は目指さなくても良い
1.カイゼンには、全社的なルールが必要
と、書くと、何を言ってるんだ、できるところ、身近なところからどんどん改善の習慣をつけろと前回(第26回)で言ってたやんか、ええ加減な奴め、と訝る方もおられるだろうが、自分の机の上や引出し、身の回りでのコミュニケーションなど、他の部門に影響しないところから始める。同僚に進めるのも良いが、では、共用の書架にある技術資料やマニュアルの並べ方を勝手に変えてしまったらどうだろう。いや、マニュアルは1巻から順番に並べるようにしたんだから、文句はないだろうと思える人は幸せだ。この分冊はオレしか使わないから、右端に置いたのに、など、良かれと思っても必ず不平は湧いてくる。そこは関係する社員や隣の部署と何らかの調整がいる。これを組織化したのがTQC,TQMであり、提案の採用、不採用を関連部署とも調整しながら、進めていけるよう、発展的に展開していけば良い。システムの改修を伴うようなカイゼンは、システム担当者が専門知識を生かして、ボトムアップを進めて行くと建設的な結果が得られるはずである。
これにはお金や資機材、スペース、試用時、習熟時の人員への負荷など、会社のリソースを注ぎ込む必要も出てくるので、経営者・管理者への働きかけも必要であろう。こうした動きが期待でき、ボトムアップが成果をあげられるのは、日本の企業の大きな強みである。
が、悪い方向に動くと得て勝手な周囲と調和しない、ヤミ改修とでも言ったら良いか?特定部門でEUCなどと称して、全体最適に合致しないシステムが出来上がってしまうこともある。
この辺のさじ加減が、経営者・管理者側にも、スタッフの側にとっても難しい。変革提案にNGを連発するのでもいけないし、良い提案だけが実践されるように持っていく、最初は小さく始めても、そうした動きを全社に広めていくと、自分の部署、部門からDXに必要なマインドセットが広がり、全社に好影響をもたらすこと期待できる。が、大抵、大きな企業ほど、何もしない防波堤(内側に向いた)のような上司がいるので、ゲンバ、提案者の側に、繰り返し見せ方を変えて提案する、ゆっくり懐柔する、理解者を見つける、などの手練手管は必要になる。喧嘩しないで、諦めもしないで、気長にやろう。(一度うまく行き始めると、加速度的にカイゼンの実行スピードは上がる。)
特に基幹システムの管理者は、全社的なシステム運用や、部門間の運用ポリシーに違いが出ないよう、統一的な運用に配慮。一部門でのUIや帳票の変革は影響が少ないであろうが、もし有用なものであれば、全社で採用した方が良いのは自明である。→最終的に、有効なカイゼンはすべからく全社・全部署に適用すべし。
2.基幹システムが悪いのか
前章での全社的なカイゼン・変革、さらにDXの体勢は一朝一夕にできるものではないし、安全性を考慮し過ぎると、結局守旧的な運用になりがちである。
2025年の崖(DX白書2018年初出)、問題も経済産業省の担当者が、あれは基幹システムの刷新が必要だと強調しすぎた。もう少しDX本質的な部分、ダイナミックケイパビリティ、トアラスフォーメーションを産む企業マインドが必要と理解して欲しいのに、と宣っていたが、巷間、基幹システムの早急な刷新が必要と受け止められ、性急に急ぎすぎたのか?工期遅延に焦ったのか?今、大手食品メーカーの「プリン」の出荷管理が止まってしまったりしている。
一連の基幹システム更新失敗の原因は、更新作業が悪い、進め方が悪い、担当IT企業が悪いのではなく、元々、安易に不統一な改修や部門単独でのカストマイズを進めたことにあると思っている。これ、2000年問題とよく考えると同じなのだ。システム全体の日付を管理するclockの桁数を増やせば良いだけであったのが、つぎはぎ改修やカストマイズの結果、どこのテーブルの日時情報をどこのサブシステムが引用しているのか、皆目わからなくなって、調査だけでも大変な工数を要することになってしまった。
もし、やり方が悪いとすれば、改修履歴、ソースコード、など、ITベンダー側のドキュメントやデータが元々散逸していて、探せない、では調査に時間をかけないといけない。そして、運用側でも要件についてどのような議論があったのか、あるカストマイズで実現した機能を引き継ぐ必要はあるのか、新バージョンでは切ってしまって良いのではないか? ユーザーとベンダーでシステム全体の現状についての認識を共有し、どのようなスケジュールで、進めるか? などといった認識合わせ、(すり合わせ)が不足だったのではないか?それで、出来るだけ早くやってしまわないと業界で遅れをとる、大変なことになる、みたいな雰囲気に巻き込まれ、いかにも拙速に慌ててやってしまったのではないかだろうか?
特に一時流行ったEUCをセクションごとに異なるベンダーに任せてちょこちょこ弄っていたようなところでは、大変なことになっているかも知れない。誰がどういう理由でどう弄って誰が仕様を知っているのかワカラナイ。
本当はカストマイズなし、国際標準の会計処理やUI、データベース構造などに合わせた、ローカルな部分を極力抑えた新たな基幹システムへの更新は今後絶対に必要なのに、今回の事件の煽りで、しばらく、基幹システムはこのまま引っ張ろう、という状態が出始めているような気がする。
図1.これはプリンではなく乾麺。
チルド、冷蔵などの保存期限によって在庫管理の方法は大きく左右される。私の愛する三輪そうめんは、出荷も順調のようである。
不幸にして障害を起こしてしまった企業は諦めずにやり遂げ、問題が早めにわかって良かった、着手が遅れれば、生産性向上のゲインが獲得できるまでにさらに時間がかかっていただろう、と前向きに捉えてほしい。
先送りにしよう、なんて動きはもっての外である。
3.RPA、ノーコードツールには意外な落とし穴が
安価で優れた営業支援ツールやB Iツールの登場で、自らが処理する業務で課題を発見し、システムを簡単にいじれるようになった。
特にGUIの部分は使いやすいように変えられるので、便利である。
ところが、全くの予備知識がない社員が、スマホを使うように作り込んでしまうと、入力規制がかかっていないか、他の機能との連携を考えていなかったりして、YYYYMMDDのデータとYYYY/MM/DDが混在してしまう。他のサブシステムに連携すると、書き直さないといけない!一旦CSVに吐き出して編集して。。など却って全体的な手間暇が増えてしまうことがある。文字コード、連携仕様、拡張可能なデータベース形式に、などシステム管理者の助言すべき項目がたくさんあるし、ノーコード、を謳っていてもローコードで、ある程度コーディングの知識が要るもの、簡単にできることがいくつかあっても、少し凝ったことをすると、そこは書き換えないと!代理店のエンジニアに委託した方が安全みたいなサービス・システムも見受けられるので、注意が必要である。システム管理者は、直接ユーザーのニーズはどこにあって、この方法でも良いのではないか?どこまで改変や大規模な造り込みが許されるか?など、やはり、コミュニケーションを取りながら、部分最適と全体最適をともに実現できるよう、調整して行くことが必要だ。
プログラム書いてるだけじゃダメ、というのが昨今のシステム担当者の辛いところかも知れない。
4.ぜひ導入を提案してほしい!リーンマネジメント
前回も書いたが、日本の3S・カイゼンは素晴らしいものである。きっちり体系化されている。が、3S・カイゼンやそれを体系化したTPS(トヨタ生産方式)は、海外に移入されて少し違った方向に発展している。デジタルとの組み合わせ、でDXを指向するところはほぼ同じだが、生産現場にとどまらず、行政機構や事務部門にも一般化され、経営者層の生産性向上や変革マインドの醸成に寄与しているのが、リーン・マネジメント。
さらに、オープンエンジニアリングという以前に、ディベート、世界的なコミュニティの創設によって、企業間で議論しながら、組織管理や事務的な業務の処理方法にまで応用が効くように展開されている。フィアット、フォルクスワーゲン、などのCEO、CDOまでがひとつところに集まって議論し、持ち帰っては議論し、次に何を変えたら成長につながるかを考える仕組みが出来上がっている。トヨタの技術者、経営者と学・官の関係者が一堂に介して、あるいはオンラインでカイゼンとでDXを語っているのである。
そこまでは無理にしても、社内でこうした議論をし、変革の進め方を決めていく。生産現場だけでなく、システム運用・改修や経営・管理までカバーする、くらいの取り組みをやっていかないと、せっかくボトムアップで変革に取り組み、組織が自働的に効率化していく仕組みがあるのに、まことに勿体無い日本の現状である。
5.完全なスマート化はめざさなくても良い
いずれもchat GPTomini (最新版)に描いてもらった。人間の介在の度合いに違いあり。
ドイツのインダストリ4.0は、ダンドリ替えやマテハン、検査まで徹底的に自動化し、人間が職人技を発揮したり、工程間ですり合わせを行ったりするなどの「スキ」を完全に無くしてしまい、いわば理詰めで生産性を上げる。仕掛品の搬送もロボット、加工はロボットとマシニングセンターなどの自動機、クルマのフロアパネルに部品を組み付けるときには、でっかいオレンジのロボットが数台がかりで車を裏返している。よく見えるし、上から作業できて効率的だ、しかし、いくら費用をかけるのだろう?
日頃のダンドリ替えはボタンひとつでできるのだが、革新的な技術が出てきたりすると、スマートファクトリー全体、工場プラント全体を入れ替えるのだろう。シーメンスのスマートファクトリーを導入した中国企業、ならそれでも良いだろうが、日本企業が真似するとケガをしそう。
中小部品メーカー、加工メーカーでは、アセンブリがなく、工程も比較少ないので、そこまでやらずとも、将来のフレキシビリティを確保しながら、職人技も残し、部分的な数値化や可視化で成功している事例も数多い。。
カイゼンへのマインドは全ての社員が持っているし、小さな仕掛品を運ぶのにはロボットでなくとも、手動のローラー台やスロープを使っているところもある。(スピードはロボットと変わらない。急ぐと人間の方が早かったりする。)手渡しで、よろしく、というような場面もあって、対話が生まれれば、ムードも良くなりカイゼンのネタも上がってくるというものである。
また、手作業もうまく残しているところも多い。管理さえデジタルでそつなくできれば、手づくりの良さが付加価値になることも多々ある。
今は被災からの再生で大変だが、輪島塗の工場がスマートファクトリーになって、ピカピカの漆器が生産できたら、誰か買いますか?
こうしたところに日本ならではの、強みを生かしたDX推進のヒントがある。
連載一覧
筆者紹介
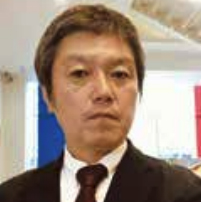
ITコンサルティング DXpower 代表
◆独立行政法人中小企業基盤整備機構機構 中小企業アドバイザー
◆公益財団法人関西文化学術研究都市推進機構 コーディネータ
◆一般社団法人エコビジネス推進協会事務局長
◆BAC 大阪
◆みせるばやお
コメント
投稿にはログインしてください